Management and the problem of motivation—part 1
By Jim Thompson (jthompson@cellulosecommunity.net or jthompson@taii.com)
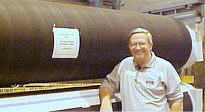
Week of 20 Aug 2007
I have spent years in this column promoting the idea that we are all employed to spin the invoice printer and slow down the check writer. Otherwise there is no reason for our position to exist. I have also often declared that the best management system is that of the military, for if you can manage people to the level that you persuade them to willingly be injured or even perhaps killed, you are a heck of a manager.
All along, though, I have been disturbed by the loss of the attitudes of our agrarian ancestors. Farmers of old and today have to be both workers and managers. They have to toil with hands and skill and also look out for the invoice printer and check writer. They have to do it all.
A couple of hundred years ago, as the industrial revolution took off, people moved from farm to factory and, later, to service industries. By default, it fell to measuring their time and attendance to determine their worth. Yes, there were rankings amongst workers based on skill and responsibility, but the underlying, baseline measurement was time and attendance. The military method of organization, with enlisted personnel and professional managers, naturally transitioned to industrial organizations. Of course, the military has never had the time measurement problem, for while in a military career, you are with your bosses 24/7, except for leaves once in a while.
At the height of the extremes of “doers” vs. “managers” unions were born to protect and represent the workers’ welfare in their relationship to management. In the United States, from about 1875 through 1975, this method was predominant. The workers, or “doers” were told what to do and measured primarily by time and attendance. They were not expected to think much.
For the last 35 years or so, there have been experiments with all kinds of systems of management and reward. Until recent times, most of them have not worked very well. So-called “gainsharing” compensation systems, in particular, have seemed to cause more angst than good, at least from what people in the field (from top to bottom of the pecking order) tell me. Likewise, systems that have driven management into the lowest ranks while at the same time destroying the old management responsibilities failed as well.
It seems as though we have yet to find a way to capture the business spirit of our agrarian ancestors. There are some hopes and hints of better ways to do this coming from, of all places, the auto industry. The Japanese and Korean automakers apparently have been especially successful at this. They are doing two things that benefit both the business and the employees equally. First, they have driven decision making down into the organization and also listen to the workers on the line when they have ideas to improve productivity and quality. Simultaneously, they have not abandon the idea that management is in charge of overall productivity and efficiency, but they have abolished the attitude that management is all-powerful and all-knowing. Often, what would have in the past been considered perks of management (corner office, private parking place) have been obliterated. Management has become, for all to see, clearly a responsibility and duty rather than a privilege.
I firmly believe successful industrial enterprises of the future will move more and more in this direction, and as they do so, will refine and enhance these ideas. The successful pulp and paper industry business of the future will have learned these lessons well.
Next week, I’ll prove that attendance is not what anyone really wants to measure and take a peek at the future of measuring performance.
Fortunately, when it comes to safety, we have for a long time all been reduced to a common basis of saving human life from harm or death. Perhaps we could take a few lessons from our safety camaraderie and apply them to the balance of the business.
Be safe and we will talk next week.
|