Get Close
Jim Thompson (jthompson@taii.com)
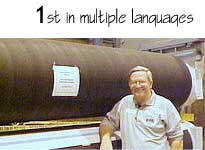
Week of 1 June 2009
Click here, then click "Trans lator" in top navigation bar for other languages. Follow Nip Impressions on Twitter
If you find yourself in charge of a mill or department ten years old or older, you have probably had a reduction in staff at one time or another. It is time to gather what's left as close as possible to the second most important machine on site--the paper machine (if you have read my work for a long time, you know the most important machine is the invoice printer).
Most likely staff reductions have left you with scattered, half-occupied office clusters. Some of them may be in other buildings. Take advantage of the vacancies and move everyone as close as you can to their respective operating departments. If you can empty satellite buildings, tear them down as quickly as possible.
My vision of the ideal office setup is in my 2005 book, "The Osage Mill." In that book, the mill manager finds an old building in the middle of the mill and moves everyone there.
In real life, I had this vision of organizing a mill's staff in this way back in the 1980's. In the 1990's a good friend of mine put it into practice. He took over a mill in a cold and wintry climate. It was an urban location. There was the old fashioned administration building across a city street from the mill. On the opposite side, across five or six railroad tracks, was a complex of trailers housing the engineering department. No one in these satellite facilities wanted to spend much time, especially in winter, visiting the actual operation, the whole reason for their existence.
After he reduced the bloated inventory, warehouse space was in abundance. He built walls around a large section of this space, painted the floor gray, the walls white and added bright lights. He sat his desk in the middle, and all departments emanated from there. No partitions. When you called there, the background noise was reminiscent of a transportation terminal.
He demolished the old admin building and removed the trailers. The system worked. This, plus a number of other changes, put the mill in record profitability territory in an otherwise lousy market.
If you have empty offices around, you can make a similar change, for the better, with a very tiny expenditure. If you have empty offices near your production departments, fill them with operational managers first. The next nearest offices should be filled with maintenance and technical personnel. The engineers come next. After that, environmental and administrative. Try to empty some buildings and tear them down immediately.
I don't think it is a coincidence that the best operating and profitable mills I have ever seen by and large keep their people close, most of the time in buildings connected to the operations. Focus your people on what is important. Say it not only in the way you conduct yourself, but in the way you have them organized.
Probably the best I have ever seen is the Kimberly-Clark mill (built by Scott Paper just before their demise) at Owensboro, Kentucky, USA. This tissue mill/converting operation was obviously planned with great care. As you come in the front door, the offices are straight ahead, with converting on one side and the machines on the other. All managers are closely connected.
I think if I ever was asked to operate a mill again, I would make sure there were no disconnected buildings, other than operating departments such as utilities, pulp and paper.
Of course, people closer to their work naturally have less chances of falling on their way to their work. This is one small way you can absolutely and conclusively improve safety--a step not taken is one in which a person can not fall. Be safe and we will talk next week.
|